На этой странице будут публиковаться статьи и заметки по эффективным технологиям, материалам, оборудовании для изготовления кабельных сборок и жгутов.
Статья №1.
Особенности применения
индукционного нагрева при низкотемпературной пайке ВЧ-кабелей. Часть 1.
1.Введение
Множество традиционных методов пайки используется во всем мире для выполнения задачи изготовления соединительных кабелей. Наиболее распространенные методы включают: проводящую пайку (например, паяльник или пламя), конвективная пайка и инфракрасная пайка. Кондуктивная и конвективная пайка требуют теплопередающей среды: твёрдое вещество или газ, соответственно, и время для передачи тепловой энергии из этой нагретой среды в заготовку. Инфракрасное излучение может обойти потребность в тепловой среде за счёт большей, менее сфокусированной области нагрева. Существуют новые способы пайки, такие как лазерное плавление или ультразвуковая пайка, которые могут обойти некоторые из этих недостатков, но с недостатками, такими как высокая стоимость, невозможность нагревания больших площадей или невозможность доступа к целевой зоне нагрева.
В отличие от вышеупомянутых методов пайки, требующих передачи тепловой энергии, индуктивный пайка припоя использует электромагнитные поля для передачи энергии непосредственно на заготовку и сам припой. Заготовка по существу становится нагревательным элементом. Это достигается путём пропускания переменного тока через точно сконструированные архитектуры катушек.
Индукционный метод нагрева проводников переменным электромагнитным полем давно и успешно применяется в промышленности. Воздействие энергии высокочастотных (ВЧ) электромагнитных колебаний позволяет осуществлять высокопроизводительный бесконтактный нагрев в различных процессах: термообработке, плавке, упрочнении, сварке, пайке, выращивании кристаллов и т. д. за счёт вихревых токов, индуцируемых в проводящих материалах.
Тепло здесь не передаётся обрабатываемой детали из окружающей среды, а возникает в ней самой в результате действия индуктированных токов. Инструментом, передающим энергию высокой частоты в спаиваемый металл, является индуктор. Он представляет собой виток или спираль из нескольких витков медной трубки, при работе охлаждаемых водой, по которым идёт ток высокой частоты. При этом вокруг витков создаётся переменное магнитное поле. Подготовленные к пайке детали располагаются в индукторе, где они пронизываются переменным магнитным полем. Переменное магнитное поле индуктирует электродвижущую силу, под действием которой в металле возникают токи, разогревающие детали до необходимой температуры.
2 Наиболее важные особенности ВЧ-нагрева
Нет оснований предполагать, что токи высокой частоты оказывают какое-либо специфическое влияние на процесс пайки, однако совершенно очевидно, что быстрый нагрев металла и интенсивное движение расплавленного припоя под действием сил электромагнитного поля активизируют флюс, улучшают смачиваемость поверхности и заставляют припой более энергично проникать в зазоры. Все это благоприятно отражается на качестве пайки.
2.1 Достоинства высокочастотной пайки
· Локализация нагрева в пределах обрабатываемой зоны
(Меньшее коробление и поводка изделия благодаря местному нагреву спаиваемых поверхностей)
Возможность быстро нагревать спаиваемый металл и производить пропайку глубинных швов за счёт выделения тепла непосредственно в самом изделии, без передачи его извне. При этом, благодаря кратковременности
· нагрева, происходит лишь незначительное окисление металла при пайке твёрдыми припоями и отсутствует окисление поверхности при пайке мягкими припоями
· Высокая производительность процесса, вытекающая из возможности концентрировать значительные мощности в малом объёме с помощью токов высокой частоты
· Получение однородной качественной пайки посредством регулировки режима нагрева и точной дозировки энергии, передаваемой в изделие, при возможности автоматизировать процесс и организовать его в потоке механической обработки.
· Высокая плотность энергия создаётся вихревыми токами непосредственно в материале, что обеспечивает высокую скорость нагрева
· Улучшение растекания припоя и перемешивание расплава металла за счёт возникновения электродинамических сил
· Улучшение и оздоровление условий, труда рабочих
2.2 Недостатки высокочастотной пайки
· Большие первоначальные затраты на приобретение высокочастотного оборудования
· Трудность пайки изделий сложной конфигурации
· Зависимость формы индуктора от формы спаиваемого шва и конструкции детали
· Источники питания.
Статья №2.
Особенности применения
индукционного нагрева при низкотемпературной пайке ВЧ-кабелей. Часть 2.
3 Улучшение качества процесса пайки и качества пайки
Выработка тепла непосредственно в рабочей детали, в отличие от промежуточной среды переноса, позволяет быстрее реагировать с индукционной пайкой. Это связано с несколькими факторами, первый из которых заключается в том, что плотность энергии, достигаемая при индукции, является чрезвычайно высокой: 100 Вт. Это значение намного больше, чем для конвекции: 0,5 Вт, излучения (электрическая муфельная печь): 8 Вт и сравнимо с паяльником: 100 Вт.
Эффективность проводящих нагревательных элементов дополнительно затруднена добавлением диэлектрика, необходимого для изоляции «живого» электрического нагревательного элемента, что требует неэффективного перегрева резистивного элемента для преодоления присущие термически резистивным свойствам электрических изоляторов.
Также индукции может улучшить процесс пайки из-за ее высокого уровня повторяемости, что обеспечивает более агрессивное время цикла. Точный контроль параметров процесса, таких как частота, рабочий цикл, уровень мощности и конструкция катушки, обеспечивают более последовательные результаты. Такое управление в сочетании с бесконтактной технологией переноса энергии индукции означает, что быстрое и последовательное достижение температуры пайки достигается более безопасно. Риск термического повреждения из-за температурных градиентов, которые происходят из-за перегрева в результате несовместимых условий контакта, таких как контактное давление, поверхностная пористость, чистота поверхности или площадь контакта, с индукцией отрицаются.
Способность быстро нагревать локализованную и целевую область в индуктивном приложении не только означает, что части подвергаются воздействию тепла в течение меньшего времени, это также означает, что смежные материалы не являются ненужными мишенями избыточного тепла. Пластиковые оболочки, печатные платы или крышки интегральных схем, например, могут страдать от искажений, поверхностной коррозии, окисления и, следовательно, потенциального разрушения в результате рассеянного тепла из конвективных и проводящих сред . Ущерб от избыточного тепла еще больше усугубляется тем, что все больше и больше кабельных сборок требуют бессвинцовых припоев, иногда даже по закону. Бессвинцовая пайка стала настолько распространённой, что средняя температура пайки увеличилась на 40 °C, что означает, что температуры плавления приближаются к максимальной температуре, допускаемой большинством самих паяных компонентов.
И, возможно, самым большим преимуществом индуктивной пайки, является повышение качества самого паяного соединения. Поскольку только целевая область нагревается, сокращая количество брызг. Разбрызгивание дополнительно смягчается за счёт участия пондеромоторных сил, влияние которых также помогает в смешивании сплавов припоя и распространении припоя на поверхности пайки. Осуществляется процесс более быстрого нагревания заготовки до температуры плавления припоя наряду с возможностью локализовать тепло к меньшей площади, как к соединению, так и к окружающим металлам и другим структурам. Эти структуры, в свою очередь, действуют как теплоотводы сразу после завершения паяного соединения, так что скорость охлаждения припоя значительно возрастает, улучшая механические свойства припоя. Поскольку скорости охлаждения ниже с индукцией, чем при конвективном переплаве и инфракрасном переплаве, образуются как более мелкие зерна, так и более тонкий межфазный слой.
4 Устройства индукционного нагрева на магнитопроводе
На данный момент существуют новые конструкции и исследованы параметры индуктирующих устройств на магнитопроводе, в которых нагрев проводящих материалов осуществляется в зазоре магнитопровода.
Прогресс в области индукционного нагрева, при монтажной пайке достигнут за счёт разработки новых конструкций индуктирующих устройств и применения новой элементной базы в ВЧ источниках питания. Нагрев переменным электромагнитным полем в зазоре магнитопровода индукционного устройства с открытой магнитной цепью обеспечивает высокую скорость при небольших удельных мощностях, однако, сильно зависит от материала детали и геометрических параметров устройства.
Для нагрева колец, небольших плат, проводов используют индукционные устройства с замкнутой и разомкнутой магнитной цепью. В первом случае нагреваемая деталь размещается вне магнитопровода, охватывая его наружную поверхность, а во втором - в зазоре магнитопровода.
Высокий потенциал автоматизации процесса индукционной пайки значительно снижается из-за возможной ошибки оператора.
Статья №3.
Особенности применения
индукционного нагрева при низкотемпературной пайке ВЧ-кабелей. Часть 3.
5 Индукционные устройства типа HIG (Harmonic Inductive Gain) с открытой магнитной цепью.
Традиционные мощные источники индукционного нагрева основаны на больших токах в индукторе при низких напряжениях и высокой частоте для генерации переменного
магнитного поля, которое создаёт вихревые токи в нагреваемой детали. Традиционные
индукционные нагревательные индукторы также конструируются из медной трубки и охлаждаются водой.
Индукционные устройства типа HIG (Harmonic Inductive Gain) компании iTherms Technologies (США) основаны на более низких токах в индукторе при несколько больших ВЧ-напряжениях, создаваемых портативными ВЧ-генераторами . HIG индукционные нагревательные устройства конструируют с помощью магнитопроводов из феррита с незамкнутой магнитной цепью, а для обмоток применяют высокоэффективный на частотах порядка 500 кГц многожильный провод Litz (литцендрат). Источники питания и индукторы имеют воздушное охлаждение, что является большим преимуществом.
HIG уже зарекомендовал себя как экономически эффективное средство для обеспечения эффективного, надёжного и повторяемого индукционного нагрева, дополняя многие из недостатков традиционной индукции некоторыми из сильных сторон резистивного нагрева. Это достигается за счет использования импульсного токового сигнала вместо синусоидального сигнала, тем самым увеличивая «эффективную» частоту нагрева.
Импульс HIG работает быстро заряжающимися конденсаторами и позволяет им разряжаться через катушку. Результирующая RLC-схема может колебаться на своей резонансной (гармонической) частоте, пока сигнал не затухает через внутреннее сопротивление заготовки. Это означает, что больше не требуется поддерживать фиксированную частоту и одновременно отменяет необходимость согласования нагрузки. Результирующий импульс богат высокочастотными гармониками, предлагающими повышенную плотность мощности для многих приложений, которые могут естественным образом колебаться до 500 кГц.
Увеличение или уменьшение выходной мощности легко достигается с помощью HIG путем простого увеличения или уменьшения частоты подачи импульса. Подача большей мощности работает естественным образом с приложениями, которые с готовностью принимают больше энергии, поскольку импульс гасится быстрее, чтобы обеспечить более быстрое время переключения. Это динамическое изменение коэффициента демпфирования, основанного на взаимосвязи нагрузки, можно также рассматривать термодинамически: большие части и части с лучшей связью служат в качестве более крупных радиаторов, через которые катушка может более легко рассеять свою энергию. Поскольку согласование нагрузки уже не вызывает беспокойства, катушки становятся одними и теми же устройствами «подключи и работай» с источником питания HIG, поскольку резистивные нагревательные элементы имеют резистивный источник питания. Это позволяет повысить гибкость конструкции катушек в отношении материалов, конфигурации, количества витков и типов проводов.
6 Пример низкотемпературной пайки ВЧ-кабеля (и других изделий) на устройстве HIG.
Индукционные устройства типа HIG применены для пайки коаксиального кабеля к коннектору при мощности нагрева 250 Вт . Время пайки – 2.5 с.
7 Снижение стоимости процесса пайки.
Минимизация количества энергии, необходимой для плавки припоя, и, следовательно, эксплуатационных затрат обеспечивается путём ориентации только на активной области пайки. Кроме того, индукционные системы являются последовательными, надёжными и легко автоматизированными, что позволяет снизить трудовые ставки. Продолжительность жизни оборудования также играет определенную роль в расходах на техническое обслуживание. Индуктивные катушки более легко сохраняют механическую целостность, поскольку они не требуются и обычно не допускаются для достижения высоких температур. С другой стороны, резистивное отопительное оборудование генерирует тепло от прохождения тока через тонкие резистивные элементы, которые подвергаются постоянному расширению и сжатию. Эта постоянная деформация приводит к развитию микротрещин на поверхности, которые проникают глубже со временем, что позволяет окислить и, в конечном счёте, разрушение. Время запуска для индукционного оборудования почти мгновенно, так как они не требуются для достижения рабочей температуры. Это означает, что индукционное оборудование на производственных линиях легче сжимается и восстанавливается для экономии затрат на энергию, что резко контрастирует по сравнению с тепловыми системами, такими как печи или паяльные горшки.
8 Итоги
Индукционные устройства на магнитопроводе способны с более высокой точностью поддерживать температуру нагрева деталей при высокой теплоотдаче в процессе пайки. В этом случае интенсивность нагрева в 2,5–3 раза выше, чем для монтажного паяльника, а скорость
нагрева зависит от коэффициента перекрытия зазора и при его оптимальных значениях
от 0,75 до 4 достигает 40 °С/с. С помощью индукционного устройства, выполненного на магнитопроводе, можно осуществлять пайку силовых контактов, разъемов
и проводов на печатные платы, коаксиальных кабелей.
В то время как конвективные, резистивные и инфракрасные технологии нагрева в течение многих десятилетий застаивались, технология индукционного нагрева стремительно продвигается вперёд. Такие разработки, как твердотельные источники питания, технология Harmonic Inductive Gain (HIG ™), позволили добиться большей и более точной подачи питания с индукцией, чем когда-либо прежде. Современные системы достаточно эффективны, чтобы обеспечить воздушное охлаждение как для источника питания, так и для катушки, что снижает затраты на капитальные и эксплуатационные расходы, однако они по-прежнему обеспечивают надёжность, ожидаемую от современных твердотельных технологий. Преимущества, связанные с качеством пайки и гибкостью процесса, надёжностью и возможностями, многочисленны.
Inner Coax Soldering Induction Heating iTherm Technologies
Обработка видео...
Статья №4.
Термотрансферная маркировка
В технологический процесс изготовления любого кабельного и жгутового изделия непременно включена операция маркировки. Она может касаться как маркировки непосредственно провода или же кембриков, которые надеваются на концы проводов, входящих в кабель для определения маршруты каждого провода при распайке на разъём. Традиционный способов нанесения маркировки-ручной. С помощью пера/кисти подходящая эмаль наносится на изделие. Также необходимо нанести защитное покрытие (ЛКП) для повышения стойкости к истиранию. В качестве преимущества такой технологии-экономичность и простота с освоении. В настоящее время появилась качественно новая альтернатива старой технологии-термотрансферная печать. Это технология печати, при которой краска с риббона (красящая лента) переносится на материал этикетки при помощи мгновенного точечного нагрева риббона в месте соприкосновения с материалом. Процесс маркировки в термотрансферных принтерах состоит из двух этапов:
1.Электронный перенос на рецепторную ленту.
2.Изображение на ленте совмещается с нагретой пластиной над проводом, после чего производится оттиск изображения на этикетку (термоусадочную трубку, ПВХ-трубку и т.д.).
Собственно маркировка наносится не непосредственно на кабель, а (например) на термоусадочную трубку, которая потом просто одевается на кабель/жгут/провод и фиксируется термофеном. Таким образом, существенно сокращается время изготовления кабельного изделия - не нужно ждать пока высохнет эмаль и затем лак.
Также, в связи с тем, что изображение формируется электронной головкой, управляемой соответствующим программным обеспечением, можно наносить маркировку практически любого изображения (размера и графики).
Термотрансферный метод печати гарантирует четкую печать с разрешением 300dpi, устойчивую к воздействию высоких и низких температур, абразивным воздействиям, спиртам, растворителям и прочим агрессивным средам.
Следует отметить очень широкий размерный спектр доступных для печати материалов. Так, например термоусаживаемая трубка, которую можно применять для маркировки жгутов имеет размерный ряд на провода от 1.5 до 40мм, что позволит перекрыть (по маркировке) абсолютное большинство всей изготавливаемой кабельной продукции на предприятии.
Вышеописанное оборудование в рамках производства предприятия может быть внедрено на следующих технологических операциях:
-технологическая маркировка проводов жгутов, обозначающих путь (маршрут) проводов от разъема к разъему.
-технологическая маркировка жгутов и кабелей путем усаживания маркированной термоусадочной трубки.
-“боевая” маркировка жгутов и кабелей путем усаживания маркированной термоусадочной трубки (взамен классической маркировке с перекрытием лаком).
-маркировка кабельных разъёмов этикетками.
Применение новой технологии маркировки кабелей и маркировочных трубок позволит уйти от ручного труда при проведении операции со всеми его недостатками: зависимостью от исполнителя, невозможностью повторяемости процесса и низкой производительностью. Среди недостатков классической технологии маркировки также следует отметить повышенную трудоёмкость, вызванную необходимостью предохранять эмаль защитным лаком. При переходе на новую технологию о нем можно будет забыть.
Подводя итоги можно отметить следующие преимущества технологии термотрансферной печати по сравнению с классической маркировкой: снижение трудоёмкости, снижение времени изготовления, высокая повторяемость процесса, универсальность оборудования (применяемость для широкой номенклатуры жгутов и других изделий). Среди недостатков можно отметить высокую стоимость оборудования, и сложности с внедрением в связи с ограниченным спектром применяемых материалов для термотрансферной печати отечественного производства.
Несмотря на указанные недостатки, новая технология позволит повысить технологичность изделий, что особенно актуально при переходе на серийное производство и широкой номенклатуре продукции.
Статья №5.
Припои для мотажа ЭРЭ.
Припои предназначены для выполнения технологических процессов лужения и пайки металлов и металлизированных материалов. По температуре плавления при пайке припои делятся на припои для низкотемпературной пайки (с температурой плавления не выше 450⁰С) и припои для высокотемпературной пайки (с температурой плавления выше 450⁰С). Условные обозначения припоев состоят из буквы “П” или букв “Пр” с обозначением основных компонентов: олово-О, свинец-С, сурьма-Cу, висмут-Ви, кадмий-К, серебро-Ср, медь-М, индий- Ин, цинк—Ц, никель-Н, галлий-Гл, германий-Г, железо-Ж, титан-Т, золото-Зл, марганец-Мц, бор-Б, фосфор-Ф, латунь-Л, алюминий-А с указанием доли основного компонента в процентах массе. При наличии драгоценного металла-указывается его количество в процентах по массе.
В технической документации на изделия, в которых применяется припой, а также при заказе припоя указывается его марка по нормативно-техническому документу и номер документа. Пример: припой индиевый ПИнОК 44, ОСТ 4Г 0.033.200. При необходимости указывается сортамент ( чушка, приток круглый, крадратный и т.п.).
Выбор марки припоя для паяного соединения производят в зависимости от назначения и конструктивных особенностей изделия, от паяемых материалов и от коэффициента растекаемости. При выборе припоя для пайки и лужения выводов ЭРЭ следует исходить из максимальной температуры пайки (лужения), указанной в технических условиях на данный электрорадиоэлемент.
Отсутствие нормативно-технических документов на припои указывает, что данные припои централизованно не поставляются и изготавливаются согласно рецептуре на месте.
Статья №6.
Флюсы для мотажа ЭРЭ.
Паяльные флюсы предназначены для использования в процессах пайкм и лужения для удаления оксидной плёнки с паяемых поверхностей и припоя, для защиты металлов и припоя от окисления в процессе пайки и снижения поверхностного натяжения на границе металл-припой-флюс. Припои могут использоваться для консервации монтажных элементов для защиты от коррозии при хранении печатных плат и ЭРЭ.
В зависимости от максимальной температуры флюсы делятся на низкотемпературные (до 450⁰) и высокотемпературные.
По коррозионному действию при испытания в камере влажности флюсы делятся на некоррозионный неактивированные (не вызывают коррозии и имеют низкую флюсующую активность, некоррозионные слабоактивные (не вызывают коррозии и имеют повышенную флюсующую активность), слабокоррозионные активированные (вызывают коррозию на площади 3-5℅), коррозионные активные (вызывают коррозию на площади 40-60℅), коррозионные высокоактивные (вызывают коррозию на всей площади).
По возможности смывания флюсы делятся на водосмываемые и водонесмываемые.
По содержанию основного компонента: на флюсы на основе буры, соединений борной кислоты, на основе хлористых солей, на основеборной кислоты.
Условные обозначения состоят из буквы Ф и сокрыщенных наименований компонентов: канифоль-К, спирт-Сп, триэтаноламин-Т, этилацетат-Эт, салициловая кислота-С, ,бензойная кислота-Б, полиэфирная смола-П,диэтиламин-Д, семикарбазид-Ск, глицерин-Гц, ортофосфорная кислота-Фс, цинк хлористый-Ц, вода-В.
Технологическими характеристиками, определяющими свойства флюсов является время смачивания припоя данной поверхности при использовании выбранного флюса.
Статья №7.
Автоматическое бандажирование жгута проводов лентой лэтсар (ту 38.103171-80)
Лента ЛЭТСАР (ТУ 38.103171-80) представляет собой электроизоляционную термостойкую самослипающуюся резиновую ленту, которая применяется в электротехнической и других отраслях промышленности в качестве электроизоляционного эластичного материала для различных деталей и узлов электрических машин и аппаратов.
Обмотка жгута проводов лентой ЛЭТСАР достаточно популярна на российских предприятиях атомной и оборонной промышленности, поскольку она обеспечивает надежную защиту жгута благодаря своей способности к слипанию. Но осуществляется обмотка лентой ЛЭТСАР вручную, что является очень трудоемкой операцией и снижает производительность жгутового участка.
Проведённое совместно со специалистами немецкой компании KABATEC GmbH & Co. KG (производитель оборудования для бандажирования жгута) тестирование ленты ЛЭТСАР позволило найти решение для автоматизации процесса обмотки жгута проводов данной лентой, благодаря которому снижается трудоемкость изготовления и повышается качество и надежность жгутовых изделий.
Решение было найдено на базе машины KTR10. На базовую модель были установлены ряд разработанных специалистами KabaTec опций, которые и позволили осуществлять одновременную обмотку жгута проводов лентой ЛЭТСАР и смотку её полиэтиленовой подложки.
В стандартной комплектации машина KTR10 позволяет проводить обмотку жгута только лентой ПВХ и ХБ с клеящимся слоем, но благодаря устанавливаемым опциям ее возможности могут быть расширены. Машина со специальными опциями может работать с ХБ лентой без клеящегося слоя, и лентой имеющей подложку (типа ЛЭТСАР), максимальный диаметр обматываемых жгутов может достигать 30 мм (вместо стандартных 20 мм), могут применяться сердечники для установки ленты размером 1´ (стандартно 1,5´ и 3´).
Обмоточная головка автоматически позиционируется в начальное положение. Машина оснащена устройством обрезки ленты. Скорость вращения головки 100 - 1000 об/мин, плавно регулируется посредством педали, скорость протяжки изделия 0-70 мм/оборот.
Статья №8.
Способы зачистки эмальпровода от изоляции.
1. Зачистка при помощи индукционного нагрева (прибор Zetta) Провод помещается в зазор магнитопровода и нажимается кнопка "Пуск", расположенная на ручке нагревательного блока. В зазоре возникает высокочастотное переменное магнитное поле, которое наводит на поверхности проводника токи Фуко. Токи Фуко разогревают поверхность проводника, при этом происходит отслаивание эмали от металлической жилы.
Интенсивность зачистки (ограничена нагревом магнитопровода):
провод ПЭТВ-2 димаетр 0.3 мм: 22 раз/мин.
провод ПЭТВ-2 диаметр 0.15 мм: 13 раз/мин.
Зачищает просто шикарно, на мой взгляд) Кнопочку нажал - готово! Остается только снять остатки лака при помощи какой-нибудь ветоши.
2.Способ снятия эмалевой изоляции с проводов/ включающий нанесение на изоляцию обрабатываемого участка провода раствора химически активного состава и нагрев провода в среде расплавленного припоя/ причем за счет исключения воздействия высоких температур на жилу провода наносят раствор состава/ мас.% :
Триэтаноламин 15-35
Глицерин остальное
Припой нагревают до 250 300 С.
3. Способ снятия эмалевой и лаковой изоляции с проводов включает нанесение на изоляцию обрабатываемого участка провода раствора химически активного состава и нагрев провода в среде расплавленного припоя/ причем химически активный состав - водный раствор ортофосфорной кислоты в следующих соотношениях/ мас.% :
Ортофосфорная кислота 20 и более
Вода остальное
4.Флюс низкотемпературной пайки, в состав которого входит примерно такое же количество ортофосфорной кислоты/ а также другие компоненты/ мас.% :
Хлористый аммоний 18-20
Ортофосфорная кислота 24-28
Тринолифосфат натрия 2-3
Борная кислота 2/5-3/5
Конденсат содового производства 3-4
Дистиллированная вода остальное
Данный флюс сложен по составу и предназначен только для пайки зачищенных от изоляции проводов.
Способ осуществляется следующим образом.
Подлежащий обработке участок провода смачивают путем окунания и помещают на подложку или наносят каплю при комнатной температуре 20+5 С водного раствора ортофосфорной кислоты. Подложка может быть/ например/ из картона/ дуба/ бука/ термостойкой пластмассы и т.д. Обрабатываемый участок провода с раствором прижимают нагревательным элементом с припоем на нем при 250-300 С. Концентрация ортофосфорной кислоты в растворе и время прижатия к проводу нагревательного элемента зависит от диаметра обрабатываемого провода и количества проволок в многопроводочной жиле/ а температура нагревательного элемента 250-300 С достаточна для разрушения и отслаивания изоляции от провода/ обработанного перед этим химическим активным составом.
При комнатной температуре 20 5 С раствор практически не воздействует на изоляцию провода. Под воздействием температуры нагревательного элемента раствор разрушает изоляцию провода/ которая чернеет и отслаивается от него и вместе с остатками раствора стекает на подложку/ а припой проникает к телу провода или между проволоками многопроволочной жилы и обволакивает ее/ обеспечивая надежное лужение/ поскольку раствор является одновременно хорошим флюсом для пайки.
Снятие изоляции с провода и его лужение можно также производить путем очередного погружения (окунания) обрабатываемого участка в раствор комнатной температуры/ а затем в расплавленный припой. Это дает возможность свести до минимума время на снятие изоляции и лужения участков провода. Однако более эффективно этот способ проявляется при снятии изоляции и лужении участков однопроволочной жилы/ поскольку в многопроволочной жиле вследствие капиллярности/ припой по отдельным проводникам/ расположенным внутри жилы/ поднимается выше обработанного раствором участка/ разрушая изоляцию и несколько снижая эластичность (гибкость) проводника.
5.Легко снять эмаль термохимическим способом, с помощью паяльника и куска хлорвиниловой изоляции. Для этого нужно протягивать конец провода между жалом паяльника, прижатым к хлорвинилу. Выделяемый от нагрева хлор очистит провод от эмали. Этот метод не заменим при снятии эмали с провода типа лицендрат, который широко применяется в радиосвязи для намотки высокочастотных катушек индуктивности. Лицендрат представляет собой много тонких проволочек покрытых эмалью и свитых в один проводник.
Статья №9.
Использование обмоточной ленты с липким слоем для обмотки жгутов.
По результатам работ по замене ленты 301В была подобрана фторопластовая лента с липким слоем для исключения вспомогательных операции при использовании ленты 301В по нарезке, проклейке (через каждые 3 витка) клеем БФ-4 и сушке. В результате проведённых испытаний в статичном (жгут неподвижен) состоянии и в динамике замечаний не выявлено. Испытания проводились автономно (на специально изготовленных для опытных работ жгутах) по программе испытаний.
Учитывая:
1. Образцы с опытной лентой соответствуют требованиям ГОСТ 23586-96 Монтаж электрический радиоэлектронной аппаратуры и приборов. Технические требования к жгутам и их креплению.
2. Использование материалов: лента П-Ф-4 ЭО/180/КО 0.070х19 ТУ 3491-007-00216412-97 позволит повысить производительность труда при изготовлении жгутов за счёт исключения подготовительной операции нарезки материала 301В на ленты и исключения операции проклеивания обмоточного материала 301В при лентообмотке с последующей сушкой в течение 24ч.
3. Использование материала: лента П-Ф-4 ЭО/180/КО 0.070х19 ТУ 3491-007-00216412-97 и лента П-ПМ/180/КО ТУ 3491-017-00216415-99 (поставляются в катушках) позволит применить средства механизации для лентообмотки что, в свою очередь повысит производительность и качество (за счёт фиксированного шага намотки) процесса лентообмотки.
4.Использование материала Ф-4ЭО в качестве обмоточного для жгутов в условиях климатических и механических воздействий регламентировано ОСТ 1 03856-79 Вязка и защита электрических жгутов летательных аппаратов.
5. Материал стоек к внешним воздействующим факторам для спец. изделий
6. Подтверждена возможность применения вышеуказанного материала в изделиях, на работу которых влияют свойства жгутов (гибкость, упругость и т.п.) в динамике.
Статья №10
Снятие изоляции с проводов
Поделюсь личным опытом по апробации инструмента для снятия изоляции с проводов – стрипперов. До недавнего времени, основным инструментом наших монтажников для снятия изоляции была электрообжигалка- нагреватель с тонкими вольфрамовыми нитями. В принципе, нареканий особо не было. Этот способ хорошо подходит для проводов маленьких сечений – 0.12, 0.2, 0.5. Однако, есть несколько неудобных моментов- вольфрамовые нити часто перегорают, требуют подключение к сети- привязаны к рабочему месту , подходят только для небольших сечений. Довольно часто возникает необходимость проводить зачистку проводов жгутов по месту- при выполнении монтажа в корпусе прибора. Плюс, сечение проводов и их внешний диаметр бывает значительно больше 0.5. Возникла необходимость подобрать простой ручной инструмент, который позволит работать в ограниченном пространстве, не будет иметь привязки к сети и работать с большими сечениями. После недолгих поисков были приобретены 4 вида стрипперов.
В качестве подопытного материалы были выбраны провода различных сечений (от 0.12 до 3мм2), различной конфигурации (-одно и –многожильные).
В ходе проведённой зачистки самолично и после месяца тестов в процессе работы монтажников (инструмент прошёл через руки 10 монтажников) был выявлен фаворит- стриппер в виде пистолета (№3 на фото). Работа с ним была признана самой эффективной с точке зрения удобства, функционала и простоты. Он позволяет качественно зачищать провода от 0.2мм2 .
Вариант №1 оказался удобен при выполнении работ на объекте (т.к. он был самый компактный). Вариант №2 позволяет работать с проводом сечения 0.12мм2 (единственный из всех), а вариант №4 оказался удобен при зачистке кабелей с несколькими жилами, т.к. он позволяет их зачищать одновременно.
По итогам работ было принято решение оснастить каждое рабочее место стриппером №3, а также приобрести остальные варианты в количестве 3шт каждого.
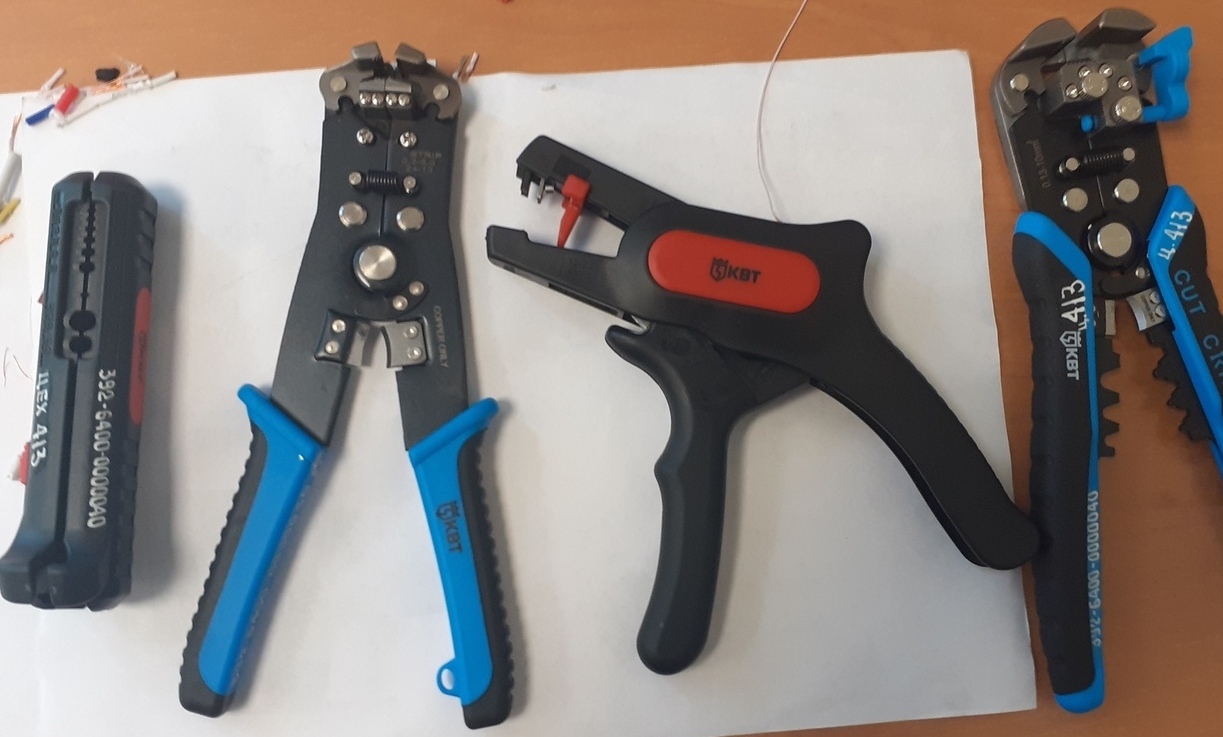
Статья №11
Извлечение контактов из соединителей
На кабельном производстве, особенно при первой сборке кабеля с новым соединителемВ приходится извлекать уже установленный пин из колодки. Кто работал, тот поймёт. Если наши отечественые соединители (например типа СНЦ23 и т.п.) экстракторы поставляют в комплекте с соединителями, то большинство импортных, да наших тоже требует специальный инструмент для демонтажа. Как правило, он идёт под дополнительный заказ под каждый вид контакта и соединителя. Плюс почти все экстракторы пластиковые и долгой эксплуатации не выдерживают. Кто-то из монтажников умудряется извлекать контакты с помощью иголки и подручных средств, но как правило при необходимости демонтажа соединитель летит в ведро. А это дефектная, перезаказ с длинными сроками и т.п. Поэтому встала задача придумать и подобрать что-нибудь достойное, простое и желательно недорогое. Соединителей у нас идёт много и номенклатура огромная и работ по демонтажу выполняется достаточно.
Порывшись, нашли наборы инструментов для извлечения пинов по 10 000р за комплект. В наборе порядка 30 инструментов на все случаи жизни под все автомобили и типы колодок и пинов. Подобрали также китайский набор для автомобильных колодок.Тестовые извлечения пинов прошел на ура.
С обратной стороны колодки, подаем немного провод с пином, чтобы фиксаторы освободились. Берем экстрактор нужной ширины. Вставляем его в колодку, при этом покачивая враво-влево, для того, чтобы фиксаторы выгнулись и дали вытянуть пин. Тянем за провод вытягивая из разъема. С этими приспособами изъятие пина из разъема занимает 15-20 секунд.
Долговечность набора вызывает подозрение, поэтому также решили заказать дорогой набор. Плюс, нашли в руководстве по эксплуатации чертежи экстракторов для соединителей СНЦ23 и СНЦ144 (что для нас Очень актуально). Будет чертить и делать у себя. По итогам работ напишу про результат с фото и чертежами экстракторов.
Статья №12
Отказ машины для зачистки ВЧ-кабеля COSMIK 48rx
Действующая схема подготовки к обработке:
1.ответственный инженер получает образец кабеля
2.по имеющемуся образцу выполняется обмер штангенциркулем всех слоёв (диаметры)
3.создается программа на основании обмеров
4.пробная обработка
5.работа по проверенной программе.
Программа для кабеля sucoform:
Первый цикл - обрез кабеля с разведением ножей до диаметра, превышающего диаметр кабеля
Второй цикл - зачистка до жилы
Третий - зачистка изолятора
Четвёртый - зачистка экрана
Пятый – зачистка внешней оболочки.
Хронология работы с машиной следующая:
1. На первом комплекте ножей было обработано около 300-350 кабелей (600-700 циклов обработки). Обработка была выполнена качественно без коррекции исходной программы.
2. Далее, в связи с обнаруженными дефектами обработки была произведена замена на новый комплект ножей (заменённые ножи имели “выкусы” в средней части режущей кромки). Выполнена калибровка оборудования по инструкции (из состава сопроводительной документации на оборудование) с использованием указанного в инструкции оборудования.
3. На втором комплекте было обработано около 25 кабелей (50 циклов обработки). Обработка была выполнена качественно без коррекции исходной программы.
4. Далее, в связи с обнаруженными дефектами обработки была произведена замена на новый комплект ножей (заменённые ножи имели “выкусы” в средней части режущей кромки). Выполнена калибровка оборудования по инструкции (из состава сопроводительной документации на оборудование) с использованием указанного в инструкции оборудования.
5. На третьем комплекте было обработано около 25 кабелей (50 циклов обработки). Обработка была выполнена качественно без коррекции исходной программы.
6. Далее, в связи с обнаруженными дефектами обработки была произведена замена на новый комплект ножей (заменённые ножи имели “выкусы” в средней части режущей кромки). Выполнена калибровка оборудования по инструкции (из состава сопроводительной документации на оборудование) с использованием указанного в инструкции оборудования.
7. На четвёртом комплекте было обработано 5 кабелей (10 циклов обработки). Обработка была выполнена качественно без коррекции исходной программы.
8. После обработки 5 кабелей (10 циклов обработки) на шестом кабеле были обнаружены дефекты обработки.
При внешнем осмотре обнаружена деформация посадочным мест для ножей и центраторов, а ножи имеют “выкусы” в средней части режущей кромки
В результате длительной переписки с поставщиком было принято решение заменить вращающийся блок фиксатора ножей. Весь ремонт обошелся в 600 т.р. Плюс блок ехал из Японии 2 месяца.
Статья №13
Защитные оболочки кабелей и жгутов.
Оплетение- монтаж проводов в изолирующую трубку или оплетку или раундинг. Раундинг проводов - это укладка. Укладывать провода можно не только в оплетку, для этого так же используют термоусадку или разные виды трубок.
Задачи:
1.Защита от механического воздействия. Оплётка поможет защитить провода от перетирания, перегибов, сжатий. Особенно это актуально к кабельным трассам, размещённым в подвижных или вибрирующих местах.
2.Температурного воздействия. Здесь важно правильно выбрать материал оплётки, и наши кабеля останутся целыми, даже проложенные и соприкасающиеся с нагревательными элементами. Например: горячими трубами.
3.Электромагнитного воздействия. Служит для защиты от силовых трасс, проходящих в непосредственной близости. Часто применяется для защиты акустических сигналов от наводок.
Материалы защитных оплёток.
1.Нейлоновая оплётка.
Защитная оболочка из нейлона сплетена из множества переплетённых волокон, благодаря чему является относительно гладкой.
Свойства:
- обладает хорошей износостойкостью, но боится острых кромок, предметов
-простота монтажа на кабель.
2.Текстильная (тканевая) оплётка.
Оболочка состоит из искусственной ткани - полиэстера.
Свойства:
- эластична, обладает способностями к растяжению
- плотная и износостойкая. Удобная в монтаже.
-выдерживает температуры от -40 до +120 С.
-не боится УФ излучения.
3.Кабельная оплётка из полиамида.
Состав полиамида (пластмассы) может изменяться для достижения определенных характеристик. При изготовлении могут добавляться стекловолокно или другие добавки..
Свойства:
-обладает огнестойким свойством.
-рабочая температура находится в диапазоне от -55 до +130 C.
-высокая стойкость к износу и стиранию.
-эластична, обладает способностями к растяжению.
- не боится и не впитывает влагу.
- устойчива к ультрафиолету.
4. Джутовая оплётка.
Текстильная (тканевая). Изготавливается из джута - натурального волокна, добываемое из растений. Для электробезопасности джут пропитывают специальными составами.
Свойства:
-позволяет "маскировать" кабель при монтаже в деревянных постройках, где проводка осуществляется открытым способом.
-кабель в джуте остаётся гибким.
-обладает хорошей износостойкостью.
-легко монтируется.
5. Металлическая защитная оплётка (плетёнка).
Изготавливается из меди с примесью других сплавов.
Свойства:
-способна выдерживать низкие и высокие температуры эксплуатации от - 100С до +250С.
-обладает достаточной эластичностью и надёжно защищает провод от механических повреждений.
-выступает в роли экрана и защищает кабельные линии от воздействия магнитных и электрических полей.
-может использоваться в помещениях с повышенной влажностью.
6. Резиновая/силиконовая защитная оплётка для кабеля.
Внутренний слой состоит из термообработанной стекловолоконной оболочки, а наружный состоит из силиконовой резины.
Свойства:
-обладает диэлектрической прочностью от 3000-4000 Вольт.
-rабель в резиновой защите остается эластичным
-выдерживаtn воздействие агрессивных сред: масел, щелочей, кислот.
- способна выдерживать температуру эксплуатации от - 60С до +220С.
-материал не горюч до 500 С.
-может использоваться в помещениях с повышенной влажностью.
7.Стекловолоконная оплётка.
Термостойкий стекловолоконный кембрик для защиты кабеля помогает сохранять диэлектрическую целостность кабельных трасс при воздействии высоких температур, суровых и агрессивных сред.
Свойства:
-диэлектрическая прочность до 1200 вольт.
-малый вес.
-обладает хорошей механической прочностью.
-негорюча.
-выдерживает эксплуатацию от -60 до +350 С.
Виды защитных оплеток.
Оплётка конструктивно может быть: сетчатая, спиральная, самозакрывающаяся, застегивающаяся.
1.Сетчатая. Выполнена в виде сетки типа "змеиная кожа". Выполняет защитные и эстетические функции.
2.Спиральная. Конструкция позволяет объединить кабели любых диаметров в жгуты. Вывод кабеля внутри спиральной оплетки возможен в любом его месте. Монтаж происходит очень быстро, а спиральную оплетку можно повторно использовать сколько угодно раз.
3.Самозакрывающаяся. Иначе их называют самосворачивающиеся или обертываемые. Подходят под уже смонтированные провода, где нет возможности просунуть кабель заново.
4.Застегивающаяся. Тоже самое, что и самозакрывающаяся, только дополнительно может иметь клеящий шов, липучку или застежку.
Статья №13
Особенности монтажа кабелей с использованием ПЭ защитной оплётки и термоусаживаемых кожухов РАЙХЕМ с подклейкой.
- При установке кожуха завёрнутая оплётка разворачивается обратно. Оплётку необходимо дополнительно бандажировать (материал ШЧПЭ 0.5) для обеспечения надевания защитного кожуха.
-Защитный кожух после термоусадки не надёжно закрепился на разъёме. Данная проблема может быть устранена либо заменой кожухом (некачественный образец), либо подклейкой кожуха к корпусу разъёма.
- В процессе подготовки проводов возникла необходимость изолировать две группы экранов дополнительной трубкой, что вызвало утолщение кабеля и, вероятно недостаточную степень усадки защитного кожуха по диаметру кабеля (что также повлияло на степень зацепления кожуха с корпусом разъёма).
- При установке кожуха завёрнутая оплётка разворачивается обратно. Оплётку необходимо дополнительно бандажировать (материал ШЧПЭ 0.5) для обеспечения надевания защитного кожуха.
- сменные насадки на инструмент для дозирования клея приходят в негодность после одного цикла использования.
- требуется маркировка проводов кабеля технологическими бирками или кембриками.
-требуется термофен с индикатором температуры и набором насадок
Резюме:
Данные материалы являются хорошей альтернативой ныне применяющейся ленты 301,а технология термотрансферной маркировки - заменой маркировки краской ЭП-140 с последующим лакированием. В качестве достоинств следует отметить:
-существенное сокращение трудозатрат на маркирование
- исключение из процесса изготовления операции обматывания жгута. Необходимо лишь одеть на провода защитную оболочку.
- ремонтопригодность. В случае необходимости кожух снимается с корпуса разъёма и стягивается вместе с защитной оболочкой.
В качестве недостатков можно отметить:
- недостаточная фиксация кожуха на корпусе разъёма
- большое время сушки клея (24ч в н.у.)
- большой расход расходных материалом (насадки для дозатора) в случае “одиночного изготовления “.
Корзина пуста
0
шт.
/
0 руб.
Оформить
Очистить